The MGA With An Attitude
MGA Guru Is GOING MOBILE - (August 16 - August 31, 2022)
Tuesday, August 16, 2022:
Contemplating whether we will put the rebuilt engine back in the car or just give it to friend in exchange for his borrowed engine. Either way is okay with him. The borrowed engine is running okay (and fairly low mileage after last major rebuild), so I'm not particularly keen on doing another engine swap for very little benefit. However, I have some concerns about the used clutch parts recently installed, and I did have in mind to replace the clutch, and didn't get it done with the hasty borrowed engine installation. I thought I was installing a new MGB pressure plate, but it turned out to be a used one, and the spigot bushing was slightly worn and not replaced. Now the clutch has a bit longer pedal travel than I was used to, and it squeals just a bit with start of engagement, and the center thrust plate is a bit loose so it may chatter a little on occasion.
I suppose I would kick myself if the clutch would crap out a few months down the road, then needing to pull the engine again at a less convenient time. So I just decided it's time to pull the engine to install a new clutch, and swap the rebuilt engine back into the car at the same time. Called British Car Specialists in Stockton, CA (nearest British car shop where I could drive to pick Up parts) to see if they might have clutch parts in stock, but no luck. So call Moss to order these parts. Approaching mid afternoon again (drats), so hurry up and get the order placed by quarter to three this time, and beg for it to be shipped out same day. I seriously doubt that will happen, so figure on Wednesday evening shipment and Friday afternoon receipt.
So now the plan is to put the rebuilt engine back together on Wednesday, then have a day off. Then pull the borrowed engine out of the car Friday morning, get the low starter back plate and flywheel swapped over along with engine mounts and a few other peripherals. When the clutch parts arrive we can get those installed and put the engine back in same day. You know about the best laid plans, now waiting for the next monkey wrench to fall.
Wednesday, August 17, 2022:
Show up at Baechler Machine in San Andreas, CA at 8:30 AM opening time to pick up the block
|
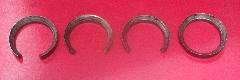
|
with new sleeves at standard size and the head with new hardened steel exhaust seats and a fresh valve job. He gave me back the new pistons and the serviceable intake valves and the worn exhaust valves, and also the old exhaust valve seats that he removed from the head. Those turned out to be cast iron inserts (that broke when being removed). So now I'm really PO'd at the prior shop that installed them and charged me for hardened steel valve seats just 6-years and 170,000 miles back, which is the only reason this head is being reworked again now.
Pay the man, and then head up to friend Stuart Mast's place in Murphys, CA to get to work assembling the engine. Navigator Elliot is getting more adept with this stuff, having had his hands inside the engine a few times by now. He seems to be taking a bit more interest in in it in recent years. Clean the heck out of the block first, then set the main bearing shells in the cradle and caps and oil it up.
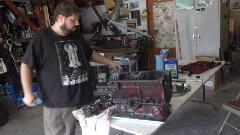
Set the crankshaft in place, install thrust washers and center main bearing cap, then the front and rear main bearings and caps, giving it a little whirl at each step to assure it still spins freely with finger tips. Then torque it down, and spin it again.
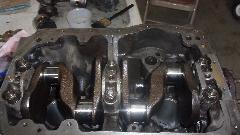
Easy to separate old pistons from connecting rods, and put the new pistons on the rods (front way around for all parts). Then the rings were a little tricky. There are County brand 5-ring pistons, which I hadn't used since the mid 90's. 5th ring at bottom of the skirt is a one piece cast iron oil wiper ring with sideways "U" cross section, symmetrical with no note for top side, no problem.
The 4th ring just above the wrist pin was a puzzler like I had never seen before. This one has a sideways "H" shape cross section with what I presume is an expander behind it. That looks like an oversize helical garter spring that will be under compression as a ring expander. Where the helical spring ends meet, half way around from the ring gap, there is a wire inside the spring like a still little cable to keep the spring ends aligned, and again symmetrical with no markings for top.
The third ring, one piece iron compression ring, definitely is marked "TOP", and there is a small notch all around on the outside bottom corner. I presume this one has a slight angle on the outside surface to initially touch at the top edge first for quick initial break in.
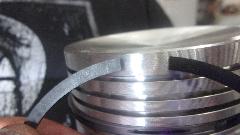
The top two compression rings are also one piece cast iron but rectangular cross section with no markings for top, so eight ring very plain. We did finally get a half decent picture of what I think is manufacturer's name logo on top of the rings just to the left side of the gap. It looks like KORI (maybe), but definitely not County.
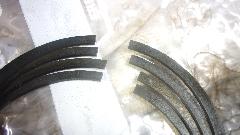
All pistons and rods installed, big ends torqued down and lock tabs turned up. No oil pump or sump yet.
Then time to install the camshaft and the engine front and rear plates.
Cleaning parts and scraping gaskets takes too much time. We found a spare engine rear plate with
low starter position in Stu's shop, so maybe wouldn't have to remove mine from the borrowed engine when it would come out of the car. That plate had lots of surface rust, so I spent time power sanding both sides (and the edges), and got it installed with a new gasket. I thought this one was maybe thinner than the original back plate, and the bolt holes were not counterbored, so I measured it. Original plate was 0.400" thick, but this one was 0.200" thick. Scratch head. That would put the engine closer to the gearbox, likely deform engine mounts and place the engine slightly farther aft. Well. install it for now anyway.
That was about the time the new exhaust valves (ordered last Friday) finally arrived, so some more cylinder head work is coming up as well.
I was painting a few things piecemeal as we went. I painted front side of the back plate below the block, and rear side of the sump before that was installed, the places with limited access after assembly.
That was when it dawned on me that the low starter position in the rear plate may be a little bit too low and too close to the block. We picked up an original MGA starter motor, and it did fit, but very close to the block (almost touching). Then picked up my little gear reduction starter, and that was not going to fit that close to the block without more modification to the flange on the GR starter. instant decision, this rear plate will have to be changed when the loaner engine comes out of the car. Painted sides of the block near the front, and inboard sides of engine mount brackets before the front plate was installed (to avoid R&R of the engine mount brackets from the front plate).
.
Then install engine front plate with engine mount brackets, cam front thrust plate, timing chain and sprockets and tensioner, and front cover with new seal and gasket. Install timing cover loose,
then install crank pulley to center the front seal, then tighten a few of the front cover bolts, remove the pulley and finish tightening all of the cover bolts.
Paint front of the engine and both sides of the front pulley before final installation of the pulley.
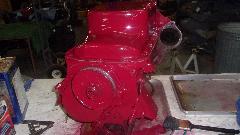
All of this while the engine was upside down without the head (fun doing the cam timing upside down). Finally installed the oil pump and screen and the sump, and painted the sump and a bit more that is easy access when inverted. That's where the engine would sit for paint to dry overnight.
We finally got to work assembling the head well after sun down (maybe 10-pm). Just one picture before we got too busy to pick the camera up again. Needed to lap the valves first, then clean it to remove all lapping compound. Something caught my attention, maybe didn't look right when lapping in the new exhaust valves, so I measured the valve heads (intake and exhaust) and wrote down the numbers for reference. Oil it up and install all the valve gear, then flip it top down level to fill the combustion chambers with water to assure no valves were leaking into the ports. Don't recall why that took so long, aside from the fact that navigator had his nose into everything (not all bad) including extra hands on the spring compressor while installing valve O-ring seals and spring caps and cotters. Seems like I didn't install umbrella seals this time, but that's okay because the factory never used them, even after the splash shields were deleted. We will see how this 18 head does in original mid-production MGB configuration.
It was pushing midnight before we packed everything up to roll, and stopped briefly at a nearby gas station for snacks and sodas before crashing for the night. Did I mention it was 100dF again this afternoon? Not so bad in the shop with a swamp cooler and a good fan, but killer outside in harsh sunlight. Much better with a bit of breeze at midnight sitting at an outdoor table with the snacks when we noticed the RF parking light was out. The RF turn signal didn't work either, so maybe lost the ground connection. Too tired to fiddle with it tonight.
Thursday, August 18, 2022:
Here are a couple pictures of the rebuilt head we finished late last night. Then it was time to finish last bits of the short block assembly, begin by flipping it right side up.

Screw in all to head studs, then go after the pressure relief valve. The old spring measured 2-3/4" long (plus two packing washers from the prior rebuild) when it should b 3". The spare spring we had in inventory was incorrect configuration with too small wire and not enough coils. Kick myself for misindexing it, as it turned out to be the spring for the hand brake thumb button. Oops. Add the correct part number to the wish list, and buy two. Then we changed two packing washers to four (two at each end) to bring it up to the correct 3" overall length. Put two fiber washers under the cap nut (as original), and good to go.
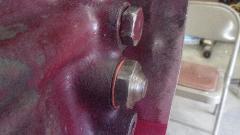
About that time the Moss parts we ordered last Friday arrived late, because they weren't shipped until Monday. Now having packages from three or four different orders, we took some time to check the contents against the invoices, and collate all the new parts (about 25 line items) into their proper nooks in inventory. The last picture is what it looks like just before they get tucked away in the tote boxes in the Magic Trailer.
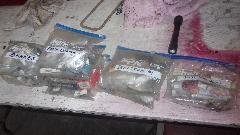
After assembling tappets, pushrods, head gasket, cylinder head and rocker shaft assembly, navigator Elliot is doing his thing with the torque wrench. Our friend (and shop host) Stuart Mast insists there should be a picture of me somewhere, as I was installing the final covers and what we thought might be a good used water pump off the shelf (because navigator couldn't find the spare one in the trailer).
One new trick for me was using Stat-O-Seal washers on the tappet cover bolts. I bought these from Moss Motors (rather expensive little buggers). The center seal is not much thicker than the steel washer, so the mating surfaces need to be flat. After hammering the metal around the center hole in the tappet cover(s) flat, I used new zinc plated bolts, one Stat-O-Seal washer, and one fiber washer under the bolt head (to make the stack height come out right).
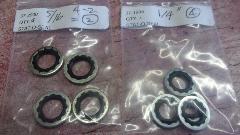
Half an hour masking and paper plugging holes, 10 minutes with a spray bomb, 15 minutes wait for partial dry, 5 minutes to pull off the masking, and there is is in all its glory. Mind you it still has the wrong rear plate, but that's easy to swap out before installation in the car.
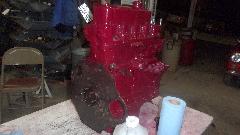
While paint was drying a bit we were cleaning up, and navigator was finally installing the nice pop-in plastic panels for the side curtains (nice change). After 11-pm it was time to roll it down the hill again, 90 minutes back to Ripon for the 24-hour truck stop with good WiFi and wall power. 10 miles from destination the left turn signals stopped working, just dead, no light. Still had brake lights and RR turn signal. Late dinner first, then some sleep, and fix it tomorrow.
Friday, August 19, 2022:
Sleep in a bit, late breakfast. Then some errands to run, but fix the RF side light first. A quick change of light bulb fixed that but then the left turn signal was intermittent, and the pilot light on the dash also quit, so maybe a bad flasher unit. Pulled a new flasher unit out of the trailer and tried to plug it in, but one of the spade terminals collapsed, so the new one was junk. Electronic Chinese junk this time. Off to an auto parts store (three in a row actually) for supplies. Bought another new flasher unit, plugged it in, and still no go. Beginning to look like a failing relay in the turn signal relay unit, no time now. Reinstall the old flasher unit, and keep the new one for a spare. A stop at Walmart for more supplies, and a stop at a bank (two of those because first one was gone). Then back to the WiFi spot for AC and a late lunch.
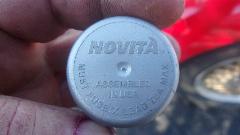
Day to catch up BBS, email and other web site business, photos and notes. Looking at weather forecasts, Saturday was going to be HOT, like 103dF, so we planned to take another day off before doing the next engine swap. Make the call and reschedule that for Sunday (when it may only 95dF).
Sometime rather late night it dawned on me that I had install the wrong exhaust valves in the cylinder head. Going back to last Friday when I had five minutes notice that I needed new exhaust valves, when I placed the rush order on the phone I inadvertently ordered valves for a 1600 engine. The loaner engine I recently touched up and put in the car is a 1600. And the one I have been driving since turn of the century is also a 1600 engine. But I forgot for the moment that one has an MGB "18" head on it with larger valves. Oops. Lots of concern, how to fix that without waiting for another new parts shipment. Sleep on it.
Saturday, August 20, 2022:
Saturday, huh? Moss not shipping on weekends. The local shop in Stockton, CA closed on the weekend. Next best option was our friend Basil Adams 110 miles away on the west coast. He didn't have new MGB exhaust valves, but he did have a serviceable set of used ones. So we gassed up the car and headed west at noon. The intended 2 hour drive turned into 3 hours of sometimes stop and creep traffic in 100+dF heat and full sun. Happy to report the cooling system was doing well with the original style cell core radiator, never went higher than 205dF peaks at the worst times. Then about a half hour before our destination the temperature gauge died (broken fluid pipe I recon). By then I had enough confidence in the radiator that I stopped worrying about it and continued on.
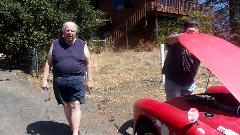
Got to Basil's place okay, still running cool. Picked up the MGB exhaust valves, had a 25 minute chat and rest, then headed back. 90 miles to Lodi in an hour and a half (no delays), then refuel again, and keep going another 75 miles or so through the valley and up the big hill to Murphys, CA. Yeah, this was supposed to be our heat day off, but needing to get the head off, replace the exhaust valves and get it back together today, so we could get on with the engine swap as scheduled tomorrow. Did I say it was hot? 102dF on the mountain, stay out of the sun and drink a lot.
Not long to pull the head off and get it on the bench. Then go after the slightly crusty but only mildly worn exhaust valves. Chuck one in an electric drill to spin it, and go at it with 80 grit emery paper on the top and neck, and 320 grit on the angled seat (don't touch the stem where it runs in the valve guide). About 5 minutes each had them cleaned up and ready to lap into the seats in the head (which was another 5 minutes each).
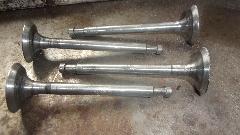
Lapping the valves into the seats took longer, being careful to check for clean buff mating ring marks all around both seats and valve heads, but the patience is worth it (and sweat equity saves money at the machine shop). Only had to lap the exhaust valves today, as the intakes were already done. Thoroughly clean the parts to remove all lapping compound (no more gritty grinding allowed). This time I did remembered to install the umbrella seals If you want to use these, the early production splash shields must be removed. When splash shields are deleted, the spring cap changes part number with larger pilot diameter to keep the inner spring concentric at top. All this was done many years ago. There is a spring base collar (like a step washer) that will center the inner spring at the bottom, while the outer spring is centered in a counterbore at the bottom. Then just push the umbrella seals home.

Install the dual springs with spring cap, and push them down with a spring compressor tool. Then install the original style seal O=rings, which fit at the bottom of the groove in the valve stem. Then install the valve cotters (split locks) which will sit on top of the O-ring. The rubber ring serves to prevent oil from running down the valve stem through the gaps in the cotters.
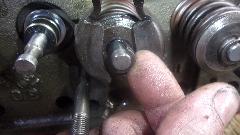
With the twin cotters in place, release the spring compressor (carefully) to lock it all together, and install the hair pin clips (just to be original, I suppose). Later production engines with type-B valve grooves and cotters do not use the clips.
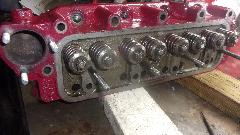
I like to check to be sure the valves don't leak. Turn the head upside down and set it level on a couple of 2x4 boards on edge. Install spark plugs to close those ports. Pour water into the combustion chambers nearly full, and wait about 5 minutes to see if any water might drip through into the intake and exhaust ports on the side. You have a right to smile when it does not leak.
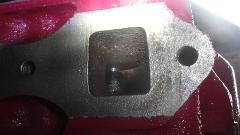
Not long to set it down on the same head gasket, which had never been wet or heat cycled, and get it torqued down (again). Then I discovered the hard way that the brand new thermostat studs from Moss are still soft (not properly hardened) and will strip the threads around 12 lb-ft torque. No more spare studs on hand, so apply a bit of sealer on the gasket, double nut the one stud that was stripped, and keep the torque down to 10 lb-ft. Note to self, order more studs (but not from Moss this time).
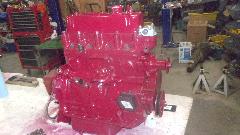
Long hot day, and we were tired, so time to knock it off and call it a night.
Sunday, August 21, 2022:
Scheduled day to at least begin doing the engine swap to remove the loaner engine and reinstall my original engine (now rebuilt). We have a pair of engine mount spacer plates recently arrived which are intended to raise the engine enough to make the hand crank fit to work again, but these will be set aside until it's time to set the new engine in the car. We have the freshly rebuilt engine, sitting on the table, and the now cooled down car getting fluids drained and engine disconnected for removal.
Then it is out, and there are two engines sitting on the table, the rebuilt one in front and the extracted loaner engine behind it with clutch already removed. Not long to remove flywheel and rear plate, get a new gasket and have the rear plate snugged up on the new engine. There is only half enough light in this shop to begin with, but this is about the time the power went of leaving us in a darker shop without the swamp cooler, one large garage door open, and working with two small flash lights when needed (which was fairly often). My favorite $30 camping flashlight is a Halogen lamp, lots of light but it eats a pair of AA batteries in an hour of continuous use. We have gone through two dozen batteries in the past few working days, and now running out of batteries (can't afford to feed the thing). And yes it is 95dF with limited breeze, but we are still in the shade.
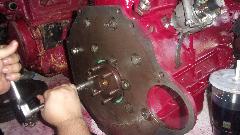
Time to R&R the new thermostat we just installed yesterday, because I found the spare blanking sleeve in the trailer and want to install it. Quick removal with one nut coming off and two studs coming out, which is okay because I finally have proper thread sealant to use (rather then the blue stuff RTV). Drop in the blanking sleeve and the thermostat (with the desired breather hole drilled in the skirt). Install the three studs, and a new Klingersil gasket, slap the cover on, tighten the nuts, and promptly strip the threads (again) on one stud while using a standard 6-incb hand wrench.
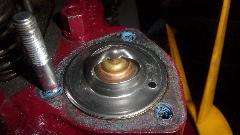
These 5/16" studs stripping at 12 lb-ft torque has been a problem for more than 10 years, and doesn't
go away. The manifold studs in side of the head have UNF fine threads on both ends (also not hardware store issue). But the very similar studs on top for the thermostat have odd threads, most likely 5/16-BSF in the head and 5/16-24-UNF threads on top end. You can't buy these studs at Ace Hardware, and after building up two engines I don't have any more spares just now. The expedient solution is to use a touch of gasket sealer, limit torque to 10 lb-ft, and double nut the one stripped thread with second nut higher up on better threads.
Unpack the new MGB clutch disc and pressure plate assembly. Good quality bits here. Semi-metallic clutch disc from Borg&Beck, very nice. The last one has run 4 years 95,000 miles and still plenty of life left. Only changing it because it is convenient now, and it may have the opportunity to run that much farther without removing the engine or gearbox again. The pressure plate is AP brand, made in Italy this time. The last one ran that far as well, but I think nearing end of life when the center release thrust pad securing grommet is loose in the spring fingers (common issue with the diaphragm type clutch). Not long to get those bolted up.
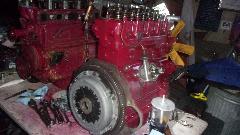
Pull a new grounding strap out of the Magic Trailer so we can leave one on the loaner engine for future convenience. Snatch my well used oil filter adapter from th loaner engine, planning on doing a hanging spin-on adapter for that one later. Snatch the hex head plug from the other engine because no spare. The story there is when I install a magnetic oil drain plug, the oil plug moves to left side of block for the oil cross port (above the pressure relief valve), and the hex head plug with copper washer from there moves to right side of block to plug the water jacket drain port (because this plug has the required shorter thread). All BSPS threads (British Standard Pipe Straight threads with copper washers), fun, huh?
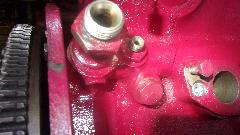
At quarter of eight PM we were just beginning to feel like we might get the engine in bolted up to gearbox and engine mounts tonight when the next monkey wrench hit the floor. I pulled the worn MGB release bearing out of the MGB fork, then picked up the new bearing just received for comparison. The new one is the cheaper one from Moss Motors (a lot cheaper), and this time I recon we got a lot less than what we paid for, another piece of Chinese junk that cannot be installed.
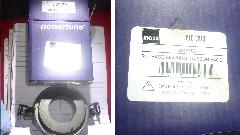
It comes with MGA stye wire clips rather than the MGB style spring steel shim clips, just the first point of suspicion to raise your eyebrows. The MGA clips will not lock into the MGB release arm (no detents in back of the arm). And it is too wide to fit into the MGB release arm cradle when mated to the correct MGB clips, so that's also a no-go.
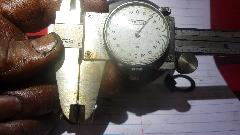
It will fit into the cradle (just) with only one shim clip, but that's a no-go too. Follow this with an hour of head scratching and cursing at Moss Motors and failing to figure out how to get it to work without bastardizing a perfectly good factory style release arm to allow use of the junk replacement part that should never exist.
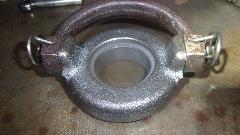
Okay, that would be a good time to call it a night and sleep on the problem, so we did.
Monday, August 22, 2022:
Good morning. Well, it was noon by the time we got started today, but on with the show. After sleeping on the problem, I have decided to do something that is generally against my morals, and bastardize a perfectly good original clutch release arm in order to use a faulty replacement part. There is a lathe available here, so I could re-machine the new release bearing to make it right, but time is precious, and it is going to be easier and quicker to hand grind the inside surface of the release arm. Measurements are like this:
|
Original bearing width = 3.075
Original shim clip thickness = 0.015 x 2
Original arm inside space = 3.108
Net clearance in assembly = 0.003
New Power Tune bearing width = 3.090
Need to increase arm space by 0.015
|
Okay, hold the fork firmly, align it squarely with side of the grinding wheel, grind until hot, dip in water to cool, measure carefully. Repeat several times until desired measurement is reached. Starting with 3.108, stopping at 3.123.
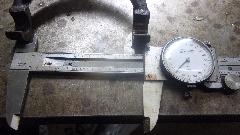
Damn, I'm good. Perfect fit. But next time I buy a new release bearing with correct dimensions, I will also have to buy a 0.025" shim washer for correct fit. How many people will have to waste time on this faulty part?
Get on with the installation, and check out the new release arm pivot bolt. 0.494 shoulder diameter is 0.004 too small for proper fit with a 0.500 ID bushing. Should be 0.498 ID for 0.002 diametrical clearance in a precision bronze bushing. 1.406 shoulder length (1-13/32 inch) is spot on for a British fractional inch dimension. (Congratulations as they used to be too long, nice fix).
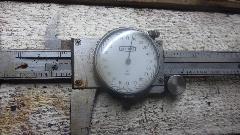
Pushing our the old worn bushing, using two standard wrench sockets. The bushing drops inside of the larger socket, while the smaller socket OD is slightly smaller than the bushing OD. Align carefully in a vice, and given a gentle squeeze it slides right out.
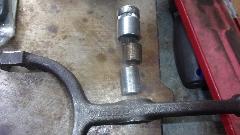
Check and oil the new bushing before installation. Standard thought is to soak the Oilite bushing in oil for 24 hours, but in fact it should pre-oiled. Just to be sure, oil it anyway. Hold upright on one finger, and fill it with oil. Put thumb over top to seal the central cavity, and squeeze to put some hydraulic pressure on the oil. In a few seconds you should see oil begin to "sweat" out of the bushing OD.meaning the porous sintered bronze bearing material is saturated with oil, good to go.
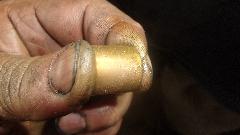
The shoulder bolt makes a good driver for the bushing, with a deep well socket on the other side, just squeeze it in the vice, and it goes together as easily as it came apart. Perfect fit.
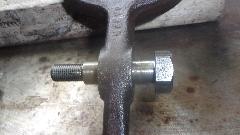
The clutch slave pushrod and clevis pin will be badly worn, so always replace those parts. Good time to replace the rubber excluder boot as well. I like to grind the release arm square end to round off the corners, making it easier to push the boot over the arm when you're under the car. All assembled once just to be sure the required part are all there and won't be lost before assembly.
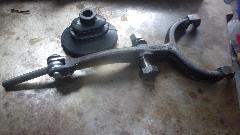
Yes, that is the old rubber boot, totally turned to sticky mush in only 4 years with exposure to oil
under the car. Obviously another faulty replacement part made with the wrong (cheap) elastomer material.
If this is the first time installing an MGB release arm in an MGA gearbox (with MGB front cover), then you would need to grind the side slot in the bellhousing a little bit for the square end of the arm to pass through. Rounding off the square corners of the arm reduces amount of grinding required (photo center above).
Install the pivot bolt and close fitting flat thrust washer and self-locking nut. You can also
install the release bearing and clips while there. Installing the rubber boot can be a bit of a fiddle underneath. I removed the clutch slave cylinder (only 2 bolts) to have easier access for my hands. If the gearbox was previously out of the car, it would be best to install these parts while on the work bench.
Finally time for the engine. Jack the gearbox up tight against top of tunnel, and tilt the engine back some. With the standard sheet metal crankshaft pulley it is a close pass, may scratch a bit of paint off of the steering rack, but it always works for me. If your engine has a harmonic balancer, no way, and you will have to remove that to clear the rack. (Excuse the ghost in that picture, might be a hair on the camera lens).
When in proper alignment, mating of the engine to gearbox is usually pretty easy. Hand brake locked and gearbox in 3rd gear so the input shaft cannot turn. Push and jiggle the engine, and turn the crankshaft slowly with a wrench. It usually slides together in 10 seconds up to a few minutes. But this one surprised us, taking more like a half hour of fiddling, including a couple of long bolts and nuts finger tight. Be patient, do not force it.

Closed up with the two alignment bolts in place. The bolt you see near the oil outlet port (upper right of engine) and the one 180 degrees opposite (lower left of engine) fit into slightly smaller clearance holes in the engine back plate and gearbox bellhousing. Put those two in first, and you can tighten them right down, and then the rest of the bolts will fly right through with no fuss.
The next three pictures represent a three hour fight. Remember the engine mount spacer plate I showed you early Sunday, just before we pulled the loaner engine out of the car? I was determined to install two of those, one on each side, to raise the engine so the stating handle (hand crank) would fit in above the steering rack, as it did originally from the factory. I suspect replacement engine mouts have been thinner than original spec for the past several years (maybe farther back). With seven bolts in, the bottom one on left side would not go, not even close. Bottom bolt firse, and at least one of the others would not go. Had to take both sides apart and start with the left side, finish on the right side. Lesson here is to always install the bottom bolt first. Two engine mounts usually take 20 to 30 minutes, could be just a little longer with one spacer plate, but two plates is a killer.
Then the fun part, giving the hand crank a whirl. Boy was that easy. Two flat wrenches on top of the steering rack demonstrate the space to spare. Plenty allowance for future engine mount sag.
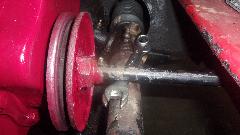
Ten PM clean up time, and not nearly as much done as I had anticipated, but I'll take it as a success all around. Clean up and head out for late might snacks and drinks before snooze.
Tuesday, August 23, 2022:
Slept in, and catching up some clerical work, so work start was mid day. Need to finish dressing the engine and get some oil into it. Going to reverse feed to prime the oil pump first, just to be sure it will prime and pump on first crank-over. The small black squeeze bottle holds 6-1/2 Fl-Oz, and we keep it around primarily for filling shock absorbers. Today it be injecting oil into the port at right rear of the engine to back fill the oil pump. The oil pump displaces 1/2 Cu-In or 0.9 Fl-Oz per turn, which is two turns of the crankshaft. Do the, and we turned the crankshaft backward 14 turns to suck in that bottle of oil. Turning forward then immediately pushes oil out of the port to prove it is well primed.
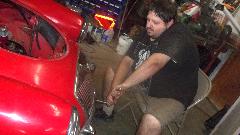
Installed a new heater valve, and then there was the crankcase breather tube connecting to the front tappet cover. Can't believe we forgot to install that immediately after engine mounts and before the manifolds, but I did manage to get it installed from underneath.
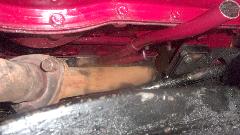
Here's a good chuckle. Stuart was picking through parts for his MGA restoration project when he picked up this heater air inlet duct stuffed up with a mouse nest. Got the engine fully dressed just before installing the radiator, then while re-checking everything noticed the fast idle link was missing. Dang those little push nuts hard to install, impossible to remove without breaking but easy to fall off when you're not looking. Had to R&R the front carburetor again to install a new link with the tiny push washer clips. Then radiator in with hoses all tight, filling with coolant just before start up, and coolant was running out on the floor. Oops. The free-spinning used water pump we picked off the shelf had a leaky seal, so pull the radiator out again and mop up all that antifreeze.
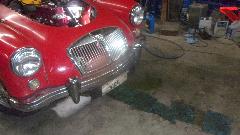
Yank out the duff water pump, and pull the good one off of the loner engine. We know that one is good, because it's the same one that was running on this engine in the car when we came limping in nearly to months ago and transferred it to the loaner engine. So now it's back home again.
Okay, radiator back in, hoses all tight, fill up the coolant and check everything again. Another leak? This time it's the temperature sensor port in the cylinder head. Since the temperature gauge had failed with a cracked fluid pipe, and the brass nut was buggered anyway, I had just cut the sensor end off and used it to plug the port in the head. Tired of dealing with the rounded off brass nut, I grabbed another failed gauge that needed to be repaired and cut that one to retrieve the sensor bulb and good brass nut to plug the port in the head. Come on, get creative in a pinch. Top up again, no leak.
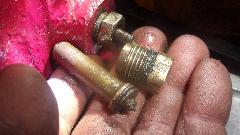
Since it just hit midnight, we weren't going to fire it up now, so knock of, clean up, and go for a late night snack before snooze.
Wednesday, August 24, 2022:
I'm sure we slept in this morning, had breakfast, checked email and a few other things. But hey, if the first picture is setting the valve lash, that means we already gave it the cam and tappets bed-in run at 2500 RPM for 20 minutes and this is the final head torque and tune-up to get it out the door. We drove it a several miles in the hills for a test run and initial run in before fine tuning the fuel mixture and idle speed. Runs like a champ as a stock 1600 with slightly shaved "18 head.
Before we put the bonnet on there are a few electrical repairs to attend to. First for the failed brake switch, easy. Pull two wires, un-screw the old one, screw in the new one (already prep'd with Teflon tape on the pipe threads), and plug the wires back on. Yup, the brake lights work.
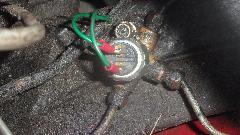
I knew what we would find in there before I cut it open, same burned contacts as all the others, because they are all the same bad design with slow make and slow break contacts.
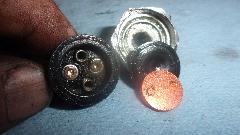
The next chore was to change the miniature relays inside the turn signal control box (for the 4th time). Last time was July 29, 2020 when they had last time they lasted 9-1/2 years, 231,544 miles, not bad. Then I changed to relays with higher temperature rating, and now one of those failed in 2yrs with only 30,485 miles. So much for higher temperature rating. But I do have some spares, so I will change them again anyway.
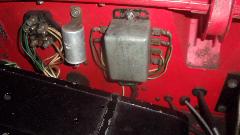
Eight quick fork lug wire terminals and two hex nuts removed from my custom captive studs, and it is out of the car in minutes. Sitting with a temperature controlled soldering iron, not long to un-solder the wires from the relays. They were mounted with double sided foam tape last time, so just a little pry with a screwdriver and they were out. None of that handy here, so this time I used super glue (and hope it will come apart next time). Takes little longer to solder all the wires back on the pins, but it is soon back in the car with turn signals working again.
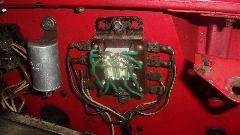
A few minutes to put the bonnet back on the car about 4:30-PM. Then spent something like 5 or 6 hours organizing spare parts and making notes for inventory records. Seems like the world got rather scrambled with several parts orders and doing two engine builds and two engine swaps in two months. Spent an hour re-organizing the shop and cleaning floors before we left around midnight.
Time for an hour and a half after midnight cruise back down the hill and through the rollers and twisties, maybe a good way to break in a new engine. Damn nice warm summer drive under the stars with a sweet running MG that handles well (nothing like the truck we were borrowing occasionally during engine work). Arrived at the Ripon, CA 24-hour Love's truck stop 1:30-am for late dinner and some WiFi time. Not getting much sleep tonight, but boy does it feel good.
Thursday, August 25, 2022:
I am posting notes for this day four days in arrears, because we just spent the prior five long days in the shop working on the car (about twice as long as it should have taken). Now there is (was) a backlog of hundreds of photos to sift through and process for this web page, and backlog of days worth of email and tech questions and BBS review, and posting a few new tech pages (in the next few days below), and a load of clerical work for the spare parts inventory list for the Magic Trailer. It will take (took) through the 29th to get caught up. Then we have at least one more day to work on the car (beginning on the 30th below). We haven't been so hectic busy for a long time.
Friday, August 26, 2022:
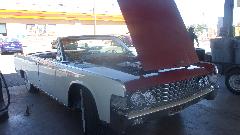
Good morning, and say hello to a nice 1065 Lincoln convertible.
-- Someone sent a write-up on repair of torn holes for front shock absorber mounting in the MGA chassis frame, so time to post a new tech page for installation of Time-Sert
threaded inserts.
-- Also added to tech page muffler dimensions and possible part numbers for replacement muffler.
-- Otherwise much of the day spent catching up photos and notes from Sunday's long hot drive and engine work.
Saturday, August 27, 2022:
Some new trivia. It now appears that some CKD cars (Completely Knocked Down) were assembled in Southern Rhodesia (news to me). That report, and some associated research, led me to post a new tech page for MGA built in that country. -- Otherwise much of the day spent catching up photos and notes from Monday's engine work.
Sunday, August 28, 2022:
Amended a tech page to show another way to repack a blown out muffler with steel wool rather than fiberglass.
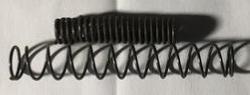
Posted two new part numbers pages for the AAA515 (or 80641) spring under the hand brake thumb button.
Monday, August 29, 2022:
Gone shopping for a couple of cheap analog temperature gauges to use a donor parts to repair the vintage gauges, oil filters and oil and other supplies. Dang hot in the central valley in California in summer, lots of parked cars with car shades in the windows, 95dF and full sun is a cooker. Back to A/C more catch up and planning. Going back to the shop for more work on the car tomorrow.
Tuesday, August 30, 2022:
Start the morning with a BIG American Car, about 1941 vintage restomod hot rod. Got the picture, but didn't find the owner. ten we were back into Stu's car shop on Murphys, CA to attend to a niggly little problem that has been bothering us since the first engine transplant when we also changes oil in the gearbox and differential. The car has been leaking one ounce of oil per day from the gearbox drain plug. Taking a close look now, there are two cracks in the housing that look like I must have over-tightened the drain plug, no idea when. Now I need to take a shot at fixing it, and I really do not want to R&R the engine and gearbox to do a gearbox housing transplant. So drain the oil and let it drip for a while, and more on this later.
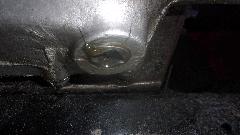
While oil was draining, we finally got around to re-installing the LF wing splash panel that was removed for the dogleg dent repair that was done Aug 8-9. Then had to R&R the rag top frame bracket (again) to reinstall the LR interior kick panel.
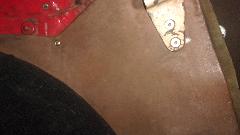
Then we got another shot at the turn signal relay. After replacing the relays and re-soldering all the wires, it was working well for five days, then went wacky yesterday. It was bewitched, doing various strange tricks, like flashing the brake lights when everything we switched off, and allowing one turn signal either left or right to work or not work, and brake lights would not work when the rear lights were flashing. We unplugged the flasher unit as a quick fix so we could drive it to the shop today (just no turn signals).
Turned out there was "snivel" (small broken single strand of wire) causing a short between two relay pins at upper right in these pictures. That was shorting the flasher input to one of the brake lamps, and since two brake lamps are electrically connected when at rest, it was flashing the brake lights. Reason it worked when parked was because I have this car rigged with 4-way flashers that work with key off. Once I found the snivel, just a slight touch knocked it out, and everything was working again.
Then we hauled out all the right tools and trinkets in preparation for repairing two failed analog temperature gauges. But one primary ingredient was missing. We could not find the multiple bits of 1/8-inch brass tubing (with 1/16" bore size) that had been kicking around in the trailer for eight years. Last time doing this was for two at once in March 2018. I know the spare tubing was still here much more recently, but not now. So cancel that project, and put the toys away. Will have to continue to drive with no functional temperature gauge for a while longer.
The gearbox had been draining for hours and was no longer dripping. A paper towel on my pinky finger could just reach inside one knuckle's worth to wipe out oil and sediment inside. Then we used a soldering acid brush with the end bent to reach in to brush it with copious amounts of lacquer thinner, literally clean enough to paint (and dry of course). There were two very visible cracks radiating from the port, making it clear where and how it could leak an ounce a day. Scratch head how to fix.

I filed off that little sharp point at the beginning lead-in of the thread. On a chance that it might do some good (or maybe not), I applied a few drops of Krazy Glue up top and down the face of the threads, hoping it might wick into the cracks. Then I mixed up some JB Kwik Weld (which is excellent stuff for patching a fuel tank), scooped some up with my pinky finger to load it up inside at top of the thread. Then walk a circle while spreading the stuff along the gearbox sump floor around the drain port. Mix up more JB stuff and smear it on the bottom around the port to cover and seal the cracks from underneath. After each step of the process, run a 1/2"-NPT tapered thread tap into the port to assure the threads will remain clean. Then we gave it a half hour to set up.
I applied a few turns of Teflon tape to the drain plug (significantly more tape than normal), and screwed it in with small torque, like wrist force from a nut driver, pretty sure not more than 5 lb-ft torque, not to spread the cracks open again. when finished I painted the plug and surrounding area with bright orange paint as a caution reminder to not over-torque the plug in the future. With some luck, maybe this will hold up without leaking again until the gearbox needs another overhaul. Refill the gearbox with oil and get it off the hoist ready to roll. Sorry I didn't get more pictures, but we were getting anxious to clean up, pack up, and hit the road.
We hitched up and headed east into the mountains on California State Route 4 toward Ebbetts Pass. Stopped briefly at a fuel stop convenience place for deli dinner, and continues on at 10-pm. Mostly up hill with lots of twisties, lots of 3rd gear hills full throttle, then lots of 2nd gear hills with even tighter twisties.
We crested the summit at 11-pm, 8738 feet altitude on the sign (although the GPS called it a little higher). Then on the steep downgrades through more tight twisties similarly 2nd gear for a while for engine braking to avoid over-using the brakes. It gradually eased off into 3rd gear downgrades, and didn't level off much more until nearly at our destination. A bit more than 80 miles through Ebbetts pas in the dark, jolly good fun (if it doesn't scare the bejesus out of you). Crossed the state line and pulled up for the night in Minden, Nevada just shy of 1-am. Hey, we are officially out of California. May plan on returning next summer for all the stuff we didn't get to do in the past two months.
Wednesday, August 31, 2022:

Good morning. We saw this same blue Ford in Minden, NV when we were going the other way on June 25th. Nice way to start the day. Need to catch up on a bunch of photos and notes today, as well as some more parts inventory detailing.
Been getting repeat phone calls from Ron Cleveland in Oklahoma who is in process of buying a derelict MGA in St Louis, MO. He has a problem trying to move it with the rear axle detached. Now it looks like we will do an extra 150 mile side trip (on our way back to Illinois) to detour through St Louis for a look and maybe try to help. Have to haul ass to do 1900 miles by Sunday.
Call to brother, just to chat. Final session on updating inventory list (tough update after doing two engines). Need to drive another 250 miles tonight (maybe), then get the 500-mile oil change for the new engine in the morning. Don't know how that's going to work out, as we may be in the middle of nowhere.
After 10-pm. three hour drive east, mostly on I-80. Car was slowing down, sputtering at high speed, not wanting to pull mild hills. Down to 55-MPH average by the time we stopped at 1-am. Suspect clogged fuel filter, not tonight.
|