The MGA With An Attitude
The Nature of STRESS CRACKS -- UT-150
With time this page may spawn multiple pages covering parts suppliers, bad parts, good parts, fatigued old parts, crack testing, and more. This is a case of a broken front suspension swivel pin on MGA. The one pictured on the right resulted in a roll on the side incident when racing an MGA Twin Cam (picture below). Most unfortunately, this happened AFTER some discussion about crack testing, and this one was not tested. Investigation after the fact revealed that it had been cracked more than half way through for some time before it broke.
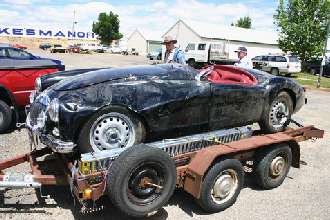
This leads to one (at least one) good lesson via the School Of Hard Knocks. A stress crack does not result in an instantaneous break, so there is (usually) time enough to detect it and fix it before a catastrophic incident.
All mechanical parts have a designed in safety factor. For instance, a non-critical structural part may have design strength of three times the expected operating load (3 to 1). Load bearing parts concerned with human life (automobiles) may have a design strength of five times the expected operating load (5 to 1). Parts subject to regular shock loads or unpredictable loading may have even higher design strength safety factor. This wide safety factor is what keeps parts from breaking the first time they are used, and hopefully for many years of normal operation.
All parts subject to periodic and cyclical loading will eventually fatigue to some extent. With time this can result in a fatigue crack. The crack will commonly start at a location of a "stress riser" feature such as a sharp corner (male or female), or at a tiny blow hole in a casting, or at a drilled hole, or at an area of reduced cross section of a part. When a fatigue crack first appears it may be of little significance, other than the fact that it is there and it can be detected with the right type of inspection. With time the crack can grow deeper, longer, or both. The larger the crack grows the more it will degrade the safety factor as strength of the structural part is being reduced. At the moment the strength to stress ratio drops below 1 to 1, the part breaks.
The good news is, time between first appearance of a stress crack and actual breaking of the part may be quite a long time. This does not mean you should ignore all parts until they break. What it does mean is that in most cases you have wide opportunity of time between beginning of the stress crack and when the part would break. This allows for occasional or periodic checking and testing of parts to detect a stress crack BEFORE the part would break. This is the first and most important lesson, that such parts should be inspected and tested for cracks occasionally or periodically. Time between inspections or tests may depending on how critical the part is, how highly stressed it is, and how likely it is that the part might break (if you know the history). More to the point, if consequences of a break may be dire (loss of life for instance), then inspections should be done more frequently to assure that it does not happen.
See also FS-204A, Stress Cracks In Suspension Parts.
|