The MGA With An Attitude
REFORMING A SWAY BAR -- FS-103F
My first sway bar was AADCO 3/4-in. It lasted 13 years, 160,000 miles (with very heavy use including race tires) until it broke. The replacement was a 7/8-in bar, originally for MGB.
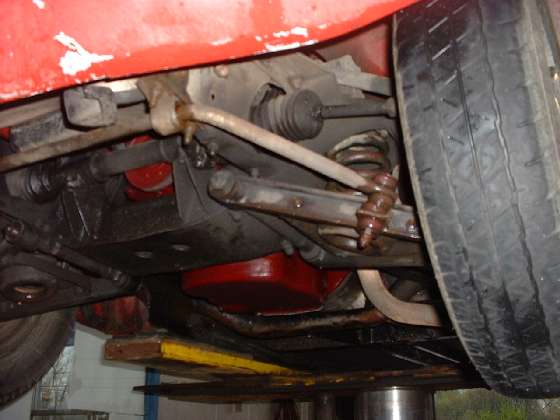
The important bit here is that I reformed this second bar to fit my need. It originally had the flat ends vertical with holes horizontal. I wanted it to have the flat ends horizontal with holes vertical. I also wanted the bends to be a bit closer together for better clearance around wide tires on full steering lock. I clamped it in a large vice, heated it with acetylene torch to bright red, and used a pipe to bend it back to straight. After doing both ends it was a long straight bar with flat ends. Then I rotated it 90 degrees and moved it down an inch in the vice before heating and bending it to the desired end shape. When finished the bends were two inches closer together, the arms were an inch longer, flat ends horizontal, both ends in the same plane, with desired distance between end holes. I then heated the entire area of the original and final bends to red and quenched it by squirting oil on it slowly with a trigger pump oil can (smelly and messy but effective).
Now anyone can go ahead and tell me I don't know nuttin out heat treatin, and I don't care. The important part is that it works for me in this case. Perhaps part of the story is that going from 3/4 to 7/8 inch diameter makes the bar 88% stiffer in torsion, so for similar loading it sees only 53% as much stress. Fact is, it hasn't broken and it is still in service after 15 years, 163,000 miles.
|