The MGA With An Attitude
BROKEN ROCKER PEDESTALS - MGA -- CH-104
A broken rocker shaft pedestal may be just a curiosity, until the day it happens to you. But with an understanding of how and why it happens, you may be able to prevent it. This is particularly important for the MGA using original type aluminum rocker pedestals, maybe less pertinent for the MGB using iron pedestals.
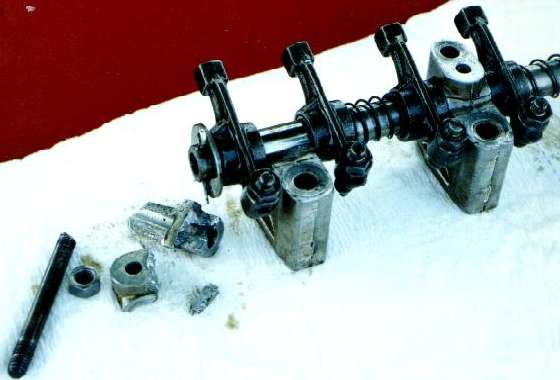
I have long since converted all of my MGA engines to iron rocker pedestals from an MGB. The impetus for that move was seeing a couple cases of fractured aluminum pedestals, one on a friend's car and once on my own car. I figured out what causes it after it happened to me.
Some person may over tighten the nuts holding the pedestals on the studs, and in particular the smaller (5/16") stud. If there is a thin or non-hardened washer used, the top of the aluminum pedestal may be deformed with a slight depression, which may reduce the diameter of the hole to nearly bind on the stud, and may cause small stress fractures to start in the aluminum pedestal. You can see in the picture that there are substantial depressions in the top of the pedestals around the mounting holes.
If the nut is too tight the stud may be pulled in tension near the yield point. The smaller studs for #1 and #4 pedestals also extend upward to accept the valve cover retaining hardware. The cover retaining nut itself is somewhat "deceptive" in that it had a (large) 5/8" hex head, but screws onto a (small) 5/16" stud. If the cover gasket leaks, a person may tighten the cover nuts too much. The tension induced by the cover nuts adds to the tension in the stud already applied by the pedestal retaining nut. The combined tension may be enough to break the stud at the top of the pedestal (at bottom of the smaller hex nut where tension is combined and stud is at smallest diameter at root of thread).
Additionally, over tightening the cover nut may also deform the top of the cover, or the spacer washer under the head of the cover nut may be left out, or the stud used may be too long. Any of these things may allow the cap nut to bottom out on the top end of the stud, after which any further effort at tightening will twist the stud and add much higher stress at the same point on the stud, at top surface of the pedestal. End result can be that the stud may break at that point.
Once the stud breaks the washer is no longer holding the pedestal down, and any small stress fractures in that area of the aluminum pedestal may more easily propagate. The upward force applied to the pedestal by the rocker shaft and valve action (springs and pushrods working on the rocker arms) will then all be applied to the one remaining stud, the larger head bolt, which increases the stress in the pedestal around the washer on the larger stud. This too may help to propagate any existing stress cracks from that location.
The top of the pedestal is relatively thin where it passes over the rocker shaft at the base of he large step on the pedestal The aluminum pedestal in particular is prone to cracking in this area. Once a crack occurs the local load stress in the part increases dramatically, and the pedestal is doomed to break and release the rocker shaft to move upward. Upward bending of the end of the shaft will dramatically increase the load on the next pedestal in line (cantilevered load), which is then very likely to break as well. By this time the end of the rocker shaft is so far displaced that the valves for the end cylinder are not opening all the way. The engine loses a lot of power like it was running on only three cylinders, and you're lucky if you can get off the road to a safe or convenient parking spot before it dies.
Been there. See picture. Notice the broken stud, the washer indentations in top of pedestals, broken #1 pedestal, and a big crack in #2 pedestal. No more aluminum pedestals in my engines, and no more problem like this in the succeeding 170,000 miles.
|