The MGA With An Attitude
Fighting FOG LAMP BRACKETS -- BP-100
May 28, 2012 - This problem has been around for a long time. The following photos and notes come from Tony Clarke who has been diligently fettling with this for some time. The fog lamp brackets were purchased from Moss Motors, October 2004 (RH) and July 2007 (LH), so the problem has been around at least that long. We all likely know that the discussion of this issue has been making the rounds of the email lists and bbs for at least as many years. A recent message from Moss Motors USA states, "only one other person has complained of fitting problems in the last 5 years". If this is true, then a lot of the blame for continuing bad parts lies with the customers who don't bother to complain or return the bad parts. If we keep on buying this junk without complaining, they will keep on selling the same crappy parts.
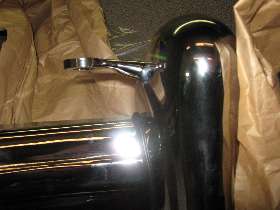
By this time Tony has had to grind some chrome off of just about every part he has touched, and it looks like he is about to grind a 1/2-inch notch in the overrider to clear the bracket and allow the overrider to seat properly against the bumper. Stay tuned for more notes to come.
These photos also have been sent to Moss Motors, and time to wait for their response. Meanwhile I can only recommend not buying this part from them until there is a satisfactory resolution to this problem. Unless of course you are willing to spend the time to modify the part to fit and have it re-chromed.
See additional comments in the Faulty Replacement Parts Report FT-051.
|